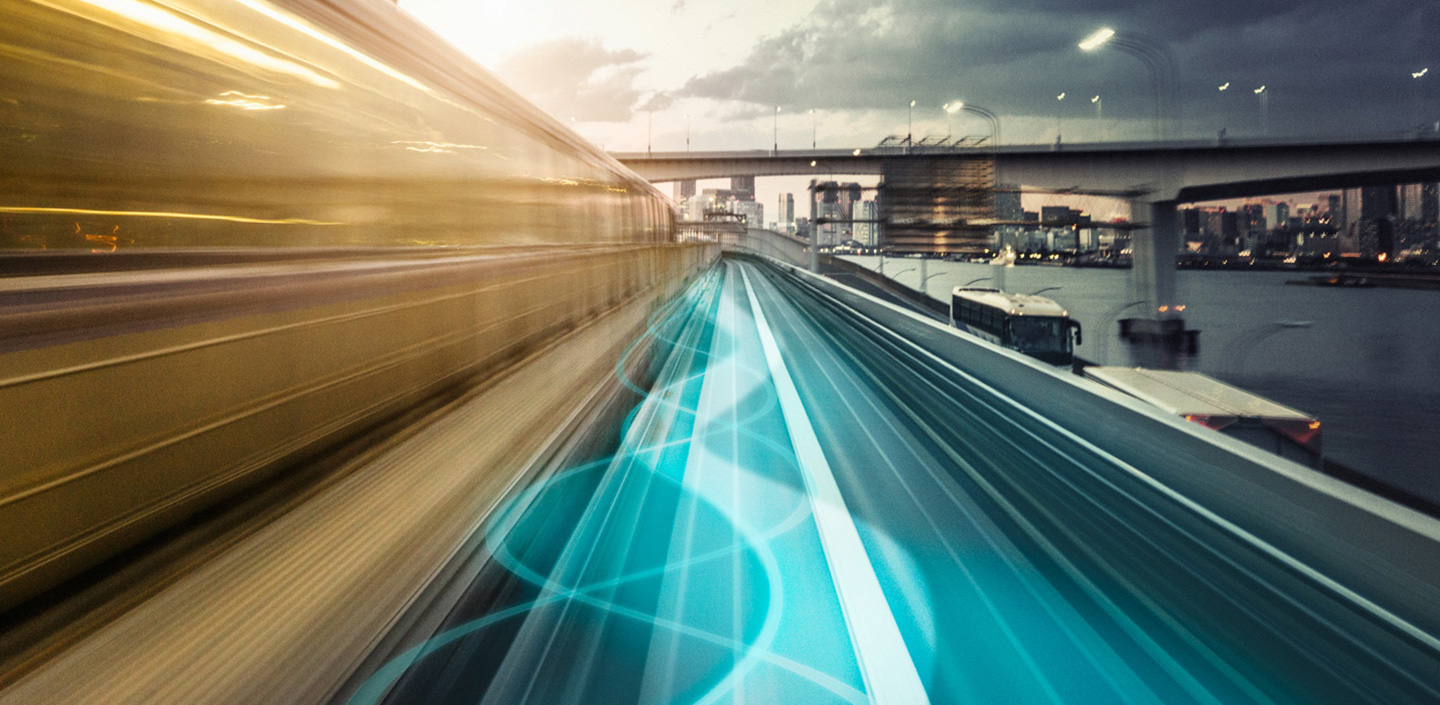
Installation of the FTS acoustic sounding system at the Belarusian Railway.
ARCHITECTURE AND PRINCIPLE OF ACTION
OPTICAL BLOCK – sends laser pulses along the optical fiber, measures backscattering intensity and transmits signals in real time.
Information Processing Block – converts signals into power spectra, classifies registered events using processing algorithms, using filters.
APPLICATION BLOCK – adds coordinates, transmits information packets to the data bank and for display on the user interface; gives out alarm signals.
BLOCK USER INTERFACE – provides a clearly structured output of information.
Experienced site | Fiber Optic Cable | Installing the pendant equipment |
Plot Dubrava – Molodechno – Smorgon, length of 72 km |
As a distributed acoustic sensor, a fiber optic fiber cable laid on a section along the railway track will be used |
The monitoring unit is installed in the Communications House at Molodechno station |
Double-track trunk line |
Over the entire length of the section the cable is laid in the ground |
|
Implemented
Installation
- The FTS monitoring unit is installed at Molodechno station.
Works connected with optical cable:
- Endpoints installed
- Optical fiber welding work completed
- At the customer’s request, the optical cable will be spliced in order to reach a length of 72 km. The system and FDU will need to be modified accordingly.
Configuring the System
- Configuration of the optical unit is completed
- The latest version (5.3.4) of the processing unit software has been downloaded.
- FTS system is active, basic configuration is applied
- The application block is configured to transfer xml to the FDU user interface
- The FDU is functioning normally
- Further configuration of the FDU and geo-calibration unit, in order to improve the accuracy of the display of passenger train stops at the stations on the FDU.
- he system is configured for remote access. Provided remote access from the office in the United Kingdom.
- The basic functionality of issuing alarms for detecting rail / wheel defects is applied.
Geo-calibration
- Collecting data for geo-calibration.
- Opto-fiber segmentation was made.
- Main geo-calibration applied.
- Further geo-calibration has been done.
- Further configuration of the FDU and geo-calibration unit, in order to improve the accuracy of the display of passenger train stops at the stations on the FDU.
Functionality testing and data collection
- Detection of defects in rails and wheels was demonstrated on the application block monitor
- The data of the FTS system was recorded for comparison with the data recorded by the customer’s vibration sensor
- The resulting screenshots showed the typical signatures of trains following the site, rail / wheel defects and normal operation of the FDU. The acoustic trace of the slider is very clearly expressed.
- Further geo-calibration has been done.
- Demonstrating to the customer the fault monitoring functionality on the application monitor and the operation of the FDU
Settings
- Work has begun on configuring defect detection and alarm reporting.
The architecture of the CAS system
Tracking the movement of rolling stock | Monitoring of the condition of devices and objects of infrastructure and rolling stock | Ensuring the protection of infrastructure and personnel |
|
|
|